Throughout history, mirrors have always been a source of fascination in different cultures. It makes sense, at least for us humans, the only animals capable of recognizing our own reflection alongside apes. The word itself comes from the Latin mirare, meaning “to marvel.” As far as we know, the oldest manufactured mirror dates back to around 6000 BC and It was found in a late Neolithic site in Türkiye. And in Ancient Egypt?
The study. This is precisely what the latest study is about. published in the Journal of Archaeological Science: Reports and carried out by a team of researchers from the University of Liverpool. The group led by Elizabeth Thomas started from a well-known idea: it was known that mirrors played a fundamental role in ancient Egypt both at a cultural and religious level, but very little was known about how they carried out the manufacturing process.
The result, as we shall see, has revealed the craftsmen’s deep knowledge of metallurgical techniques and the use of mainly three types of alloys in manufacturing: arsenical copper, copper and tin alloy, and a ternary alloy of arsenical copper with tin.
Chemical analysis. Thomas said that before starting work they studied the known facts. Namely, in Ancient Egypt, mirrors were highly polished copper, bronze or gold discs that represented the sun and whose handles were shaped like papyrus stems or the figure of Hathor, an Egyptian goddess associated with beauty and rebirth.
So the first thing they did was Analyze the metallurgy of nineteen Egyptian mirrors covering a wide chronological period from the Old Kingdom to the Late Period. This was made possible by the technique of scanning electron microscopy with energy-dispersive X-ray spectroscopy (SEM-EDX), allowing the chemical composition and microstructure of the ancient artefacts to be analysed, ultimately revealing secrets about their construction that have remained hidden for thousands of years.
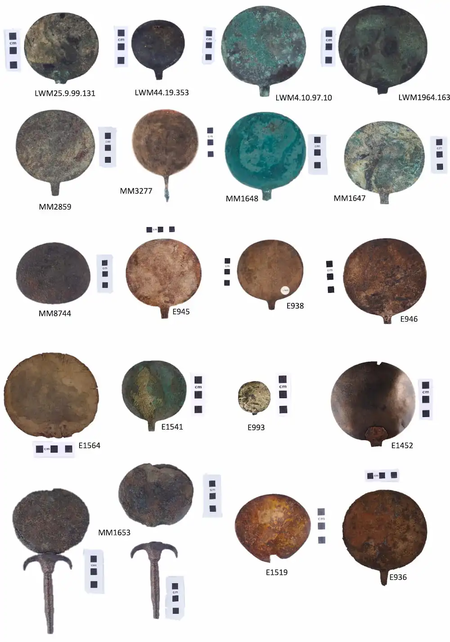
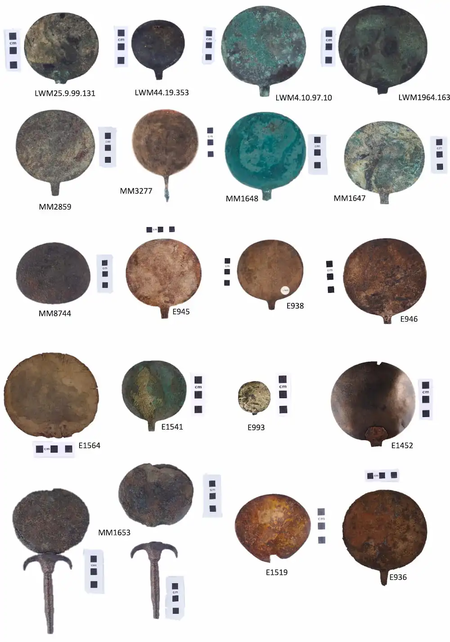
Mirrors analyzed
The three keys. As we said, the first thing they discovered is that the artisans of Ancient Egypt almost always used Three types of alloys in mirror manufacturing: arsenical copper, copper-tin alloy, and a ternary alloy of arsenical copper with tin. In addition, the study details that the composition was repeated, with around 5% arsenic or tin in the mirrors analyzed.
What does this mean? The team suggests that it indicates a high degree of control and standardisation in the manufacturing process, one far higher than previously known. Indeed, such consistency, in addition to confirming how “good” Egyptian craftsmen were at their jobs and the technical skills they possessed, led researchers to ask other questions. For example, why that specific alloy and not another?
A possible answer. Although it remains a hypothesis, Thomas and his team believe, based on everything they found, that the particular composition was due to its optimal physical properties, such as hardness and malleability, or perhaps even the resulting colour of the metal. This is no small idea, as this is how they were able to produce that golden or silvery tone in the finished mirror.
In fact, in the work there is evidence in the mirrors analyzed of a technique known as surface enrichmentwhich involves the creation of a surface layer rich in arsenic, the same that would have given the mirrors that shiny, silvery appearance, perhaps trying to give them an appearance similar to those of greater value, for example, made of silver.
Process of a prodigious technique. This type of metallurgical technique, Thomas explains, of surface enrichment, was most likely achieved through a process known as reverse segregation, a sophisticated technique that required intricate knowledge of the metallurgical properties of arsenical copper. As for the choice of alloys, it is suggested that religion could be key in the decision to use gold or similar highlights.
Finally, the work also found something surprising. Microscopic analysis revealed clues to a type of process unsuitable for the time, one where highly standardized manufacturing involved repeated cycles of cold hammering and annealing. Such a technique would have increased the hardness of the metal, allowing for better polishing and a clearer, more consistent reflection.
Yes, it seems that the Egyptians had a well-oiled artisanal metalworking “industry” long before we imagined.
Image | Public Domain, Science Museum, Elizabeth Thomas
At Xataka | We have found an Egyptian observatory from 2,500 years ago. It helps us understand their dominion over the stars
At Xataka | The largest mirror-covered building in the world is called Maraya and is (of course) in the Saudi Arabian desert
Add Comment